Restarting Abrasive Blasting
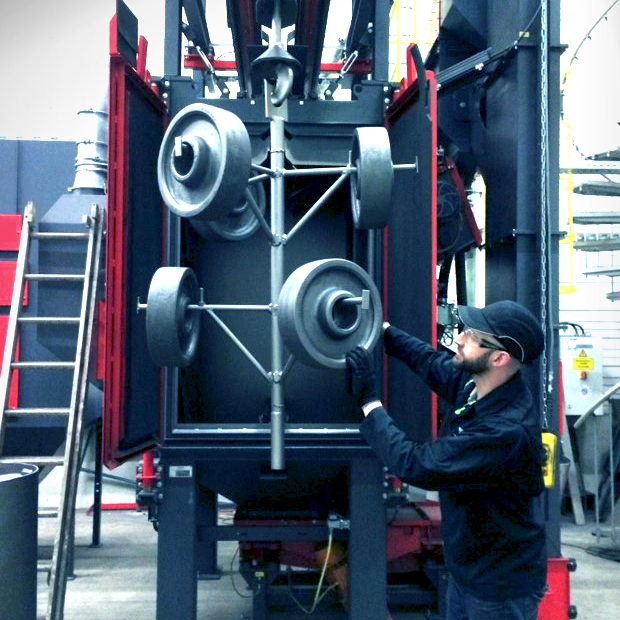
Top Tips
After longer than usual pauses in production, it may be necessary to make an inspection of shot blast equipment prior to restarting.
• Mechanical and electrical checks as recommended by your machine manufacturer or maintenance process.
• In particular, manually check the operation of blast wheels, air nozzles and abrasive media transportation system.
There should not be large quantities of abrasive in these at start up. A number of checks can be carried out on the abrasive and its recycling system.
These will improve the ability of a shot blast operation to meet its production targets more quickly. Not only that, but if checks are not performed there can be an increased risk to both health and safety, and damage to the machine.
• Check abrasive quality, removing any large clusters which may have formed due to moisture.
• Hopper level should be minimum ¾ full (ideally higher).
• Any hopper additions should be a mixture of new and reclaimed abrasive.
If only new abrasive is available then a run in period may be required before normal performance is achieved.
• Confirm sieves and mechanical parts of the air wash separator are clear and functioning correctly.
• Ducting used for air flow should be checked for blockages.
• Check and clean if necessary the filter system and dust collector.
A newly restarted machine should be monitored closely, with the usual scheduled production checks in place.
If you have any questions regarding your steel or stainless steel shot and grit, please don’t hesitate to contact the Ervin team.