Low Dust Air Blasting
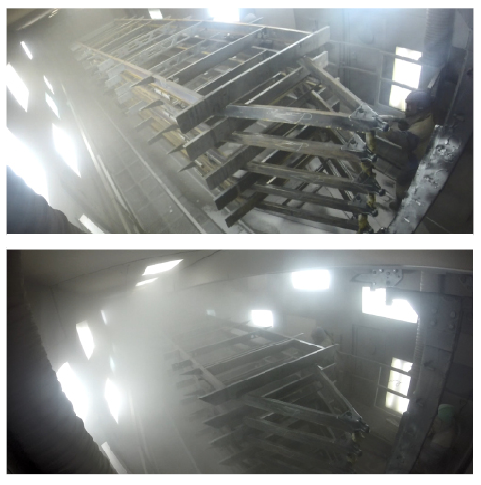
What is dust?
Dust generated during air blasting, often referred to as sandblasting, comes from the breakdown of both, the abrasive being used, and work piece being cleaned to prepare the surface for subsequent coating.
Why is it bad?
High levels of dust within a blast booth or hand cabinet is usually an indication of short abrasive life. This reduced life directly translates to greater consumption ultimately resulting in increased operating costs. Indirect cost increases include diminished dust filter performance and other consumables such as nozzles, hoses and tank parts. There is also an associated environmental impact to high abrasive consumption. Every tonne of abrasive used leads to another tonne of waste generated to be disposed of, increasing not only the overall cost of the process but its cost to the environment. Increased amounts of dust in the atmosphere also creates sub-optimal working conditions for the blaster and in surrounding processes. This results in reduced efficiency and operator morale. As a direct consequence, poor visibility will also lead to either insufficient cleaning or overblasted surfaces.
Which abrasives create most dust in air blasting?
Expendable mineral abrasives which can only be re-used up to 10 times, such as aluminium oxide, garnet, slag and glass beads have the quickest breakdown rates, and therefore create the most dust. With the availability of a well-designed reclaim system, it is prudent to consider several, better-recyclable abrasive alternatives.
What are the alternatives?
Recyclable steel and stainless steel grit can often be reused often over 800 times. Their gradual breakdown rate generates much less dust and minimizes the issues related to high levels of dust generated during blasting.
What are the other benefits?
Although the initial buying price per tonne is higher, the investment can pay back within the first year. This is especially true when taking into account consumable spare parts (metallic grits are much less aggressive on nozzles and hoses) and waste disposal. Operating costs are a combination of abrasive cost and that of consumables. Metallic abrasives are less aggressive on nozzles, and hoses and lead to reduced dust generation (and disposal). This cost reduction far outweighs the higher initial cost of steel abrasives. Field data has shown paybacks in less than a year even after taking into account the installation of a proper media reclaim system retrofit to your blast machine. Combinations of lab tests and field trials have demonstrated the overall operating cost with stainless steel grit to be between 10 to 30 times lower than with the use of aluminium oxide. These trials were validated by comparable values of speed and quality of cleaning with both media types. Moreover, better repeatability and consistency of surface profile were achieved with metallic abrasives when compared to their mineral counterparts.
Steel vs Stainless Steel Grit
Comparable sizes of (high carbon) steel and stainless steel grit have similar cleaning abilities. A quality stainless steel grit has the advantage of lower consumption, lower dust generation and reduced waste disposal requirements, with a resulting clean and rust-free surface. Both offer significant process cost reductions when compared with expendable abrasives such as Aluminium Oxide.