07 Jan A Balancing Act
“9 out of 10 shot blasting problems are caused by an unbalanced operating mix”. You’ve heard that quote, right? You also probably thought it was one of those made up statistics to make the person delivering it sound clever. Well, the thing is, it’s pretty much true – in both cases! The real figure is probably around 8 or 9 out of 10 but the importance of an operating mix cannot be denied. Let’s look a little closer.
Shot wears down during use – even the highest quality stuff. Or perhaps I should say especially the highest quality stuff. Cheap, poor quality material will fracture and lead to high consumption, whereas good shot wears down in layers. Kind of like peeling the layers of skin off an onion – only with less tears. As it wears down it gets removed by the air wash separator and filtration unit of the shot blast machine, only to be replaced with small amounts of new material that is added. You then have a range of large, medium and small particle sizes, all doing their own job. The large particles are bringing the real cleaning power, giving high impact due to their mass. Unfortunately these big guys aren’t as nimble at getting in smaller areas and leave gaps between their impacts, so they don’t cover all the surface. This is where the medium and fine particles come in. They fill in the gaps between the larger impacts and difficult to reach corners of the work piece. However too many of these can leave you lacking in impact – like taking a thousand pea shooters to a tank battle. So, like most things in life, it’s about striking a balance.
Now you understand if your operating mix is full of large particles (coarse) you will have good impact but poor coverage. If you have a fine operating mix the opposite applies. But there is also another matter to consider, and that is the number of individual particles in the operating mix. Depending on the size of the abrasive, 1 kg of the mix will contain a certain number of particles. A bigger size (or more coarse mix) will have fewer particles than a smaller finer size. Consider it this way: how many basket balls can you hold in your hand? One, I hope? Then consider golf balls. 3? 4? Then marbles, then peanuts. Then those tiny little steel like balls your Grandma would put on cakes when you were a kid that you thought you would break your teeth on. You get the picture. There are so many more impacts with a balanced operating mix providing coverage. To put it in numbers, straight out of the bag S390 (1mm) has around 205,000 pellets per kg, and a balanced operating mix 950,000. Nearly 5x the amount – and no I haven’t counted them myself! So all that abrasive, falling out of the holes in your machine? That’s the good stuff, much better than the shot or grit that’s just been delivered as that is mainly 1 or 2 sizes. That’s not even taking into account the fact that the abrasive in the machine has work hardened a couple of Rockwell points to make it even better at cleaning. Not having a degree in metallurgy, I won’t try to explain that one, but trust me – it happens, and it helps!
"9 out of 10 shot blasting problems are caused by an unbalanced operating mix"
Keeping a balanced view of your operating mix also helps you control a number of other factors. Abrasive consumption and machine wear (especially the wheel blades that need regularly replacing) can be adversely affected with the wrong operating mix. If you are also coating the work piece after blasting, a poor operating mix makes a big difference to the various values of surface roughness profile achieved. A few µm here and there on your Rz and peak count may not seem like a lot, but it can seriously undermine the coatings ability to not only stick to the surface, but to protect it from all those nasty air/water/chemical/salt combinations. The last thing you want is peeling paint on your nice new shiny surface!
So hopefully you appreciate the value of a balanced operating mix. But how to control and monitor it? Frequent additions of small amounts of material should really be all you need, but also pay attention to material being lost – to the separator and filter discards, to leaks and carry out with blasted work pieces. Also beware an abrasive supplier who will send you material that is not the size you ordered and is often too big (I know?! Who’d do that, right?). If this happens, it can reduce the cleaning ability of the shot blasting system (for the reasons described above), whilst also increasing abrasive consumption and possible providing an unsuitable surface for coating. To monitor an operating mix you can do a full sieve analysis with 5 or 6 different sieves and a representative samples from your separator. All our Ervin sales team and technicians provide that as standard for their customers. But you don’t want to mess around with that. A simple way for you and your operators to monitor daily is with the Ervin Spot Check Kit. It’s really easy, takes 5 minutes and even an idiot can do it (I’ve done it multiple times!). I won’t go into detail, but there’s a great video from our colleagues in the US and more information on our website. Or just let me know if you want a bit of assistance. After all that is my job!
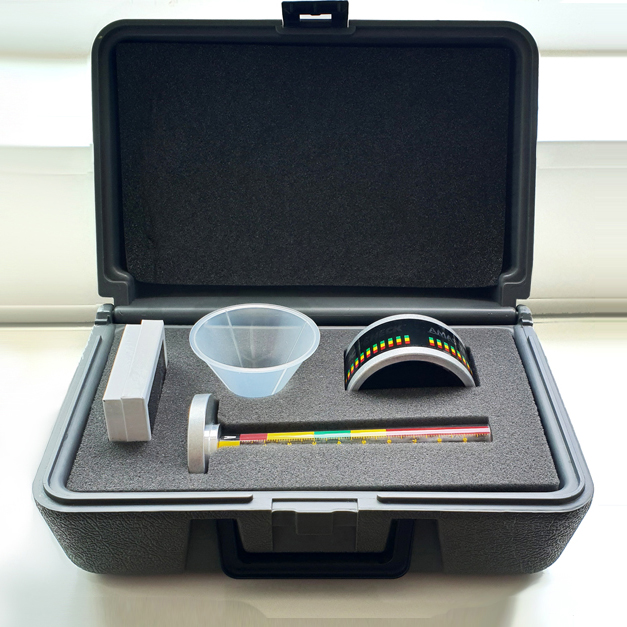