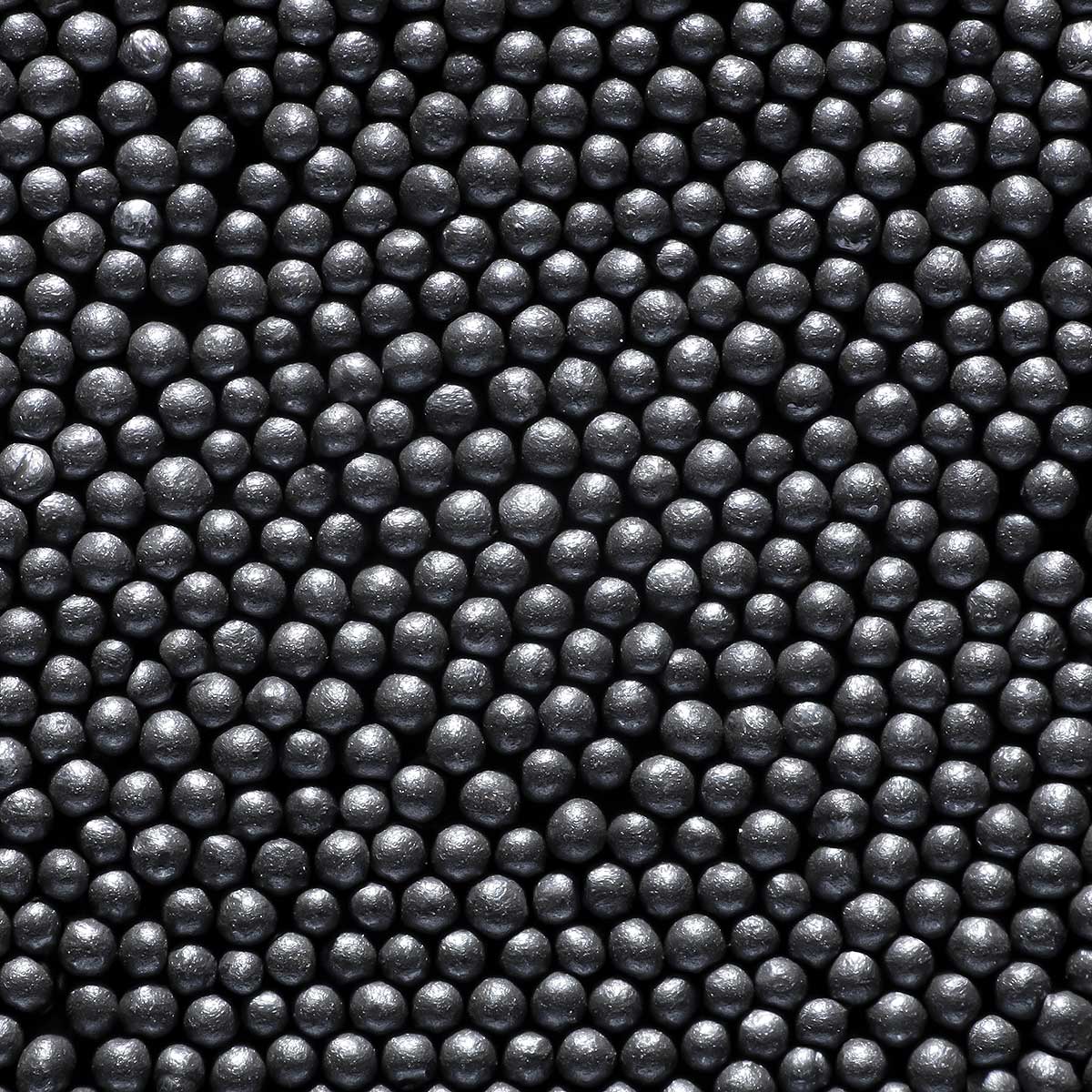
Ideal For
- Automatic wheel blast machines
- Air blast systems
- Shot peening
Applications
- Aerospace
- Automotive
Some of the key benefits you can expect when using AMAPEEN are:
The Ervin technology for high carbon steel abrasives is the most advanced in the world. Our production to SAE and AMS specifications in Glaubitz, Germany, ensures AMAPEEN shot is a consistently high quality martensitic peening media.
Continuous quality control, in combination with the cutting-edge production process, guarantees consistently high performance.
Abrasive for peening is not a commodity. It is an essential component in a technical process that can be very costly if not maintained and supported on a regular basis.
Our trained technical support personnel are therefore at your disposal, at no additional cost. We can arrange to visit relevant plants as required on a regular basis to provide:
C | 0.80 - 1.20% | |
---|---|---|
Mn | (S70 to S130) | 0.35 - 1.20% |
(S170 & S190) | 0.50 - 1.20% | |
(S70 to S130) 0.35 - 1.20% (S170 & S190) 0.50 - 1.20% (S230 and above) | 0.60 - 1.20% | |
Si | 0.40 - 1.50% | |
S | 0.05% MAX | |
P | 0.05% MAX |
S Shot | 40 - 51 HRC (390 - 530 HV) |
---|---|
M Shot | 47 - 56 HRC (470 - 610 HV) |
L Shot | 54 - 61 HRC (570 - 720 HV) |
AMS R | 45 - 52 HRC (446 - 544 HV) |
AMS H | 55 - 62 HRC (595 - 746 HV) |
Uniform tempered martensite |
≥ 7.0 g/cm³ |
SHOT | mm | 2.800 | 2.360 | 2.000 | 1.700 | 1.400 | 1.180 | 1.000 | 0.850 | 0.710 | 0.600 | 0.500 | 0.425 | 0.355 | 0.300 | 0.180 | 0.125 |
---|---|---|---|---|---|---|---|---|---|---|---|---|---|---|---|---|---|
SAE | 7 | 8 | 10 | 12 | 14 | 16 | 18 | 20 | 25 | 30 | 35 | 40 | 45 | 50 | 80 | 120 | |
S780 | AP | 85% MIN |
97% MIN |
||||||||||||||
S660 | AP | 85% MIN |
97% MIN |
||||||||||||||
S550 | AP | 85% MIN |
97% MIN |
||||||||||||||
S460 | AP | 5% MAX |
85% MIN |
96% MIN |
|||||||||||||
S390 | AP | 5% MAX |
85% MIN |
96% MIN |
|||||||||||||
S330 | AP | 5% MAX |
85% MIN |
96% MIN |
|||||||||||||
S280 | AP | 5% MAX |
85% MIN |
96% MIN |
|||||||||||||
S230 | AP | 10% MAX |
85% MIN |
97% MIN |
|||||||||||||
S170 | AP | 10% MAX |
85% MIN |
97% MIN |
|||||||||||||
S110 | AP | 10% MAX |
80% MIN |
90% MIN |
|||||||||||||
S70 | AP | 10% MAX |
80% MIN |
90% MIN |
SHOT | mm | 2.800 | 2.360 | 2.000 | 1.700 | 1.400 | 1.180 | 1.000 | 0.850 | 0.710 | 0.600 | 0.500 | 0.425 | 0.355 | 0.300 | 0.180 | 0.125 |
---|---|---|---|---|---|---|---|---|---|---|---|---|---|---|---|---|---|
SAE | 7 | 8 | 10 | 12 | 14 | 16 | 18 | 20 | 25 | 30 | 35 | 40 | 45 | 50 | 80 | 120 | |
S780 | AP | 85% MIN |
97% MIN |
||||||||||||||
S660 | AP | 85% MIN |
97% MIN |
||||||||||||||
S550 | AP | 85% MIN |
97% MIN |
||||||||||||||
S460 | AP | 5% MAX |
85% MIN |
96% MIN |
|||||||||||||
S390 | AP | 5% MAX |
85% MIN |
96% MIN |
|||||||||||||
S330 | AP | 5% MAX |
85% MIN |
96% MIN |
|||||||||||||
S280 | AP | 5% MAX |
85% MIN |
96% MIN |
|||||||||||||
S230 | AP | 10% MAX |
85% MIN |
97% MIN |
|||||||||||||
S170 | AP | 10% MAX |
85% MIN |
97% MIN |
|||||||||||||
S110 | AP | 10% MAX |
80% MIN |
90% MIN |
|||||||||||||
S70 | AP | 10% MAX |
80% MIN |
90% MIN |
AMS SHOT |
mm | 4.000 | 3.350 | 2.800 | 2.360 | 2.000 | 1.700 | 1.400 | 1.180 | 1.000 | 0.850 | 0.710 | 0.600 | 0.500 | 0.425 | 0.355 | 0.300 | 0.180 | 0.125 |
---|---|---|---|---|---|---|---|---|---|---|---|---|---|---|---|---|---|---|---|
SAE | 5 | 6 | 7 | 8 | 10 | 12 | 14 | 16 | 18 | 20 | 25 | 30 | 35 | 40 | 45 | 50 | 80 | 120 | |
S930 | AP | 2% MAX |
50% MAX |
90% MIN |
98% MIN |
||||||||||||||
S780 | AP | 2% MAX |
50% MAX |
90% MIN |
98% MIN |
||||||||||||||
S660 | AP | 2% MAX |
50% MAX |
90% MIN |
98% MIN |
||||||||||||||
S550 | AP | 2% MAX |
50% MAX |
90% MIN |
98% MIN |
||||||||||||||
S460 | AP | 2% MAX |
50% MAX |
90% MIN |
98% MIN |
||||||||||||||
S390 | AP | 2% MAX |
50% MAX |
90% MIN |
98% MIN |
||||||||||||||
S330 | AP | 2% MAX |
50% MAX |
90% MIN |
98% MIN |
||||||||||||||
S280 | AP | 2% MAX |
50% MAX |
90% MIN |
98% MIN |
||||||||||||||
S230 | AP | 2% MAX |
50% MAX |
90% MIN |
98% MIN |
||||||||||||||
S190 | AP | 2% MAX |
50% MAX |
90% MIN |
98% MIN |
||||||||||||||
S170 | AP | 2% MAX |
50% MAX |
90% MIN |
98% MIN |
||||||||||||||
S130 | AP | 2% MAX |
50% MAX |
90% MIN |
98% MIN |
||||||||||||||
S110 | AP | 2% MAX |
50% MAX |
90% MIN |
98% MIN |
||||||||||||||
S70 | AP | 2% MAX |
50% MAX |
90% MIN |
98% MIN |
AMS SHOT |
mm | 4.000 | 3.350 | 2.800 | 2.360 | 2.000 | 1.700 | 1.400 | 1.180 | 1.000 | 0.850 | 0.710 | 0.600 | 0.500 | 0.425 | 0.355 | 0.300 | 0.180 | 0.125 |
---|---|---|---|---|---|---|---|---|---|---|---|---|---|---|---|---|---|---|---|
SAE | 5 | 6 | 7 | 8 | 10 | 12 | 14 | 16 | 18 | 20 | 25 | 30 | 35 | 40 | 45 | 50 | 80 | 120 | |
S930 | AP | 2% MAX |
50% MAX |
90% MIN |
98% MIN |
||||||||||||||
S780 | AP | 2% MAX |
50% MAX |
90% MIN |
98% MIN |
||||||||||||||
S660 | AP | 2% MAX |
50% MAX |
90% MIN |
98% MIN |
||||||||||||||
S550 | AP | 2% MAX |
50% MAX |
90% MIN |
98% MIN |
||||||||||||||
S460 | AP | 2% MAX |
50% MAX |
90% MIN |
98% MIN |
||||||||||||||
S390 | AP | 2% MAX |
50% MAX |
90% MIN |
98% MIN |
||||||||||||||
S330 | AP | 2% MAX |
50% MAX |
90% MIN |
98% MIN |
||||||||||||||
S280 | AP | 2% MAX |
50% MAX |
90% MIN |
98% MIN |
||||||||||||||
S230 | AP | 2% MAX |
50% MAX |
90% MIN |
98% MIN |
||||||||||||||
S190 | AP | 2% MAX |
50% MAX |
90% MIN |
98% MIN |
||||||||||||||
S170 | AP | 2% MAX |
50% MAX |
90% MIN |
98% MIN |
||||||||||||||
S130 | AP | 2% MAX |
50% MAX |
90% MIN |
98% MIN |
||||||||||||||
S110 | AP | 2% MAX |
50% MAX |
90% MIN |
98% MIN |
||||||||||||||
S70 | AP | 2% MAX |
50% MAX |
90% MIN |
98% MIN |
Special sizes are available upon request.
SHOT: SAE J444 & J827
AMS SHOT: AMS 2431/1 & 2
AP = All Pass
MIN = Minimum
MAX = Maximum
Our sales office can guide you through the quotation process. Please call +49 30 400 37846, visit the contact page or complete the form below.
If you are considering working with a hard-wearing material, there is often no better choice than selecting high carbon steel abrasive solutions. This allows you to effectively strip or prep the material in question and undertake highly efficient peening – enabling you to produce an end-product that is truly fit for purpose.
This ability to reliably strengthen and prepare materials makes carbon steel abrasives perfect for sectors where performance and reliability are often a matter of life and death. This includes a range of industrial applications but makes it especially effective for the automotive and aerospace industries.
An essential part of metal treatment for a range of sectors, peening involves the use of percussive force to strengthen a sheet or piece of metal, making it more tolerant to damage for its unique use case. This helps prevent the material from suffering the microcracks that occur as a direct result of compressive stress – massively increasing its tolerance for fatigue and overall lifespan.
While this was originally applied to materials via a peening hammer, modern technology allows us to strike the product with metal shot through a range of methods – helping to increase effectiveness, strength, and ensure the highest possible standards of efficiency.
This makes it essential for the automotive and aerospace sectors, with both operating under the strictest of professional standards; letting materials be put into use that are lighter, harder wearing, and fit for purpose.
Shot peening materials provide invaluable help to a range of sectors where metals and materials need to be extensively prepared and strengthened before they are fit for peening.
Depending on the final use of the material being peened, this allows users to deploy a range of tools. This can include automatic wheel blast machines or air blast systems, both manual and automatic, to help provide control over the application of the substrate.
Combining hard-wearing utility and comprehensive cost-effectiveness, high carbon steel and strengthened shot blasting is perfect for workpieces of all sizes (especially in the automotive and aerospace industries), ensuring the highest standards of professional excellence and reliability when it truly matters most.
When it comes to choosing products like Amapeen for your internal work, there are a number of key benefits that should never be ignored.
These include
Quality and Cost Effectiveness – The gains made in total blasting process costs and productivity are considerable with carbon steel shot abrasive. The blasting media is always of the highest quality, ensuring optimum results and cost effectiveness.
Safety: When deploying Amapeen the slower breakdown reduces the dust levels thereby reducing the inhalation risk to your employees and ensuring that you and your teams are safe, no matter how uniquely the abrasive elements are deployed. All our shot is produced in adherence with SAE and AMS regulations – resulting in the highest possible standards for safety.
Low Consumption: Simply put, it takes less to do more with Amapeen. This allows you to significantly save on purchasing costs and empower you to get more production for less effort.
Comprehensive Support: Our team understands the importance of expert guidance when it comes to deploying shot blasting techniques in any sector. We are happy to work with you to provide additional professional help and ensure that – no matter the project – our staff are on hand to help troubleshoot any issues you may have.
Why choose us?
At Ervin, our team works with you to find a practical solution that suits your bespoke needs. If you want to learn more about what shot peening product may be right for you, check out our comprehensive solutions finder to ensure that your approach is right for your project.
Or if you need additional help and guidance, please feel free to get in touch with our team directly and let us know exactly what you need to deploy a fit for purpose solution to your project.
Select the application type you’d like solutions for
Contact our experienced sales team to discuss your requirements.
ContactNotifications