Pneumatyczna obróbka strumieniowo-ścierna o niskiej zawartości pyłu
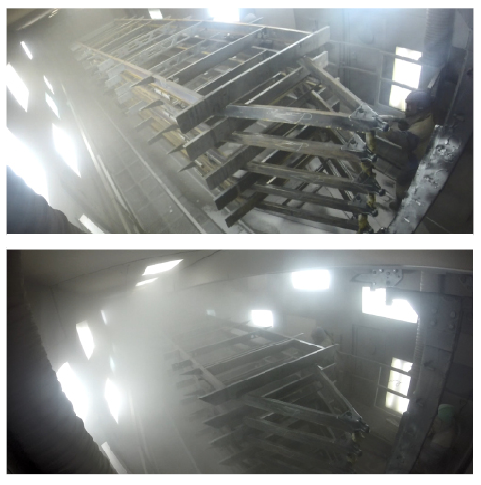
Co to jest pył?
Pył powstający podczas pneumatycznej obróbki strumieniowo-ściernej, często określanej jako piaskowanie, pochodzi z rozpadu zarówno używanego ścierniwa, jak i obrabianego przedmiotu, który jest czyszczony w celu przygotowania powierzchni do późniejszego pokrycia.
Dlaczego jest szkodliwy?
Wysoki poziom zapylenia w kabinie do obróbki strumieniowej lub w komorze ręcznej jest zazwyczaj oznaką krótkiej żywotności ścierniwa. Ta skrócona żywotność przekłada się bezpośrednio na większe zużycie, co ostatecznie prowadzi do zwiększenia kosztów operacyjnych. Wzrost kosztów pośrednich obejmuje zmniejszenie wydajności filtra pyłowego oraz innych materiałów eksploatacyjnych, takich jak dysze, węże i części zbiornika. Z wysokim zużyciem ścierniwa wiąże się również wpływ na środowisko. Każda tona zużytego ścierniwa prowadzi do kolejnej tony odpadów do usunięcia, zwiększając nie tylko ogólny koszt procesu, ale i wpływ na środowisko. Zwiększona ilość pyłu w atmosferze stwarza również nieoptymalne warunki pracy dla operatora obróbki strumieniowo-ściernej i otaczających go procesów. Skutkuje to obniżeniem wydajności i morale operatorów. Bezpośrednią konsekwencją słabej widoczności jest również niedostateczne lub nadmierne oczyszczenie powierzchni.
Które ścierniwa generują najwięcej pyłu podczas pneumatycznej obróbki strumieniowo-ściernej?
Trwałość szybko zużywającego się ścierniwa mineralnego („blast to waste”) o wysokim współczynniku rozpadu wynosi typowo do 10 cykli, ścierniwa takie jak tlenek aluminium, garnet, żużel i kulki szklane mają małą trwałość, co prowadzi do powstawania większych ilości pyłu niż w przypadku ścierniw stalowych. Przy dostępności dobrze zaprojektowanego systemu odzyskiwania rozsądnie jest rozważyć kilka lepiej poddających się recyklingowi innych rodzajów ścierniwa.
Jakie alternatywy są do wyboru?
Poddający się recyklingowi śrut łamany ze stali i stali nierdzewnej może zostać ponownie użyty często ponad 800 razy. Jego stopniowe tempo rozpadu generuje znacznie mniej pyłu i minimalizuje problemy związane z wysokim poziomem zapylenia podczas śrutowania.
Jakie są inne korzyści?
Chociaż początkowa cena zakupu za tonę jest wyższa, inwestycja może zwrócić się w ciągu pierwszego roku. Jest to szczególnie prawdziwe, gdy uwzględni się zużywające się części zamienne (metaliczny śrut łamany jest znacznie mniej agresywny dla dysz i węży) oraz utylizację odpadów. Koszty operacyjne są kombinacją kosztów ścierniwa i materiałów eksploatacyjnych. Ścierniwa metaliczne są mniej agresywne dla dysz, węży i prowadzą do zmniejszenia wytwarzania (i usuwania) pyłu. Osiągnięta dzięki temu redukcja kosztów znacznie przekracza wyższy początkowy koszt ścierniw stalowych. Dane wykazały zwrot kosztów w okresie krótszym niż rok, nawet po uwzględnieniu instalacji właściwego systemu odzyskiwania ścierniwa w urządzeniu do obróbki strumieniowo-ściernej. Połączenie badań laboratoryjnych i prób w terenie wykazało, że całkowity koszt eksploatacji przy użyciu śrutu nierdzewnego jest od 10 do 30 razy niższy niż przy tlenku aluminium. Próby te zostały potwierdzone przy porównywalnych wartościach szybkości i jakości czyszczenia z użyciem obu typów mediów. Ponadto przy użyciu ścierniw metalicznych w porównaniu z ich mineralnymi odpowiednikami uzyskano lepszą powtarzalność i spójność uzyskiwanego profilu powierzchni.
Staliwny Śrut Łamany vs Nierdzewny Śrut Łamany
Porównywalne grubości śrutu łamanego ze stali (wysokowęglowej) i stali nierdzewnej mają podobne zdolności czyszczące. Zaletą wysokiej jakości śrutu łamanego ze stali nierdzewnej jest mniejsze zużycie, mniejsze zapylenie i mniejsza utylizacja odpadów, a co za tym idzie — czysta i wolna od rdzy powierzchnia. Oba zapewniają znaczną redukcję kosztów procesu w porównaniu do ścierniw szybko zużywających się, takich jak tlenek aluminium.